창원 ‘LG스마트파크’ 가보니
10분 뒤 미리 예측해 부품 적시 조달AI·로봇·5G 접목해 자동화율 65%
자재 공급시간 25%·고장 96% 줄어
로봇팔 한 라인서 냉장고 58종 생산
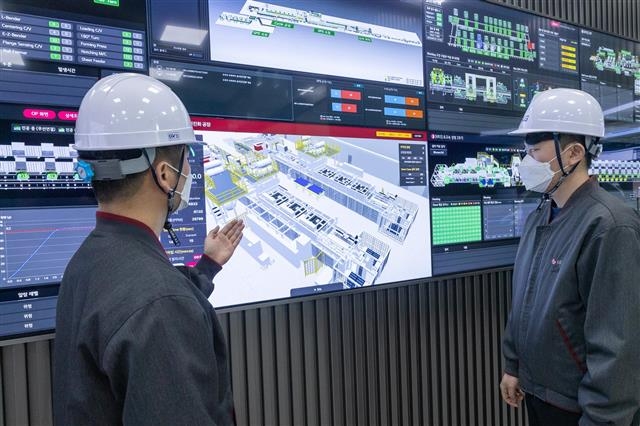
LG전자 제공
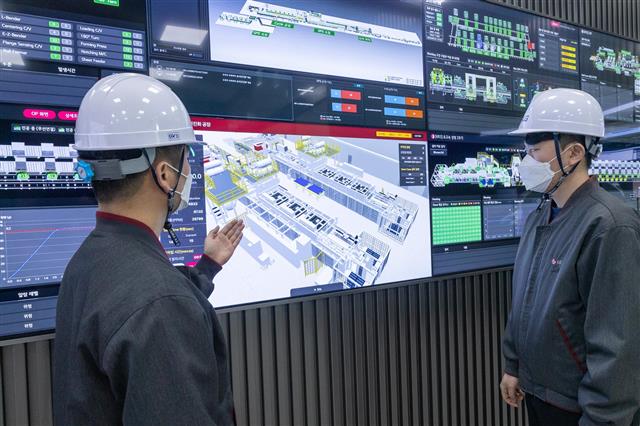
세계 제조업의 미래를 밝히는 공장을 의미하는 ‘등대공장’에 선정된 창원 LG스마트파크는 디지털 트윈 기술로 구현한 가상의 생산라인을 통해 10분 뒤의 제품 생산과 부품 이동, 재고 상황, 설비 이상 유무까지 예측할 수 있다. 사진은 통합생산동 1층에서 대형모니터를 통해 공장 가동 상황을 점검하고 있는 LG전자 관계자들의 모습.
LG전자 제공
LG전자 제공
육상에서는 5G 센서를 장착한 물류로봇이 최대 600㎏의 적재함을 싣고 무인창고와 생산라인을 오가고 있었다. 주행 중 동선에서 사람이나 장애물을 감지하면 즉시 주행을 멈추고 비켜 달라는 의미의 경고 멜로디가 흘러나왔다. 로봇이 전달한 부품은 물류 엘리베이터가 전해 받아 천장 쪽으로 들어 올리고, 이어 고공 컨베이어에 연결된 부품 상자가 최대 30㎏씩 나눠 담아 각 부품이 필요한 라인으로 전달했다. 물류자동화를 통해 자재 공급시간은 자동화 이전 대비 25% 정도 단축됐고, 설비 고장에 따라 작업이 중단되는 시간은 96% 수준으로 급감했다.
3차원(3D) 카메라와 연동된 1.9m 크기의 대형 로봇팔은 LG전자의 냉장고 생산 능력을 세계 최고 수준으로 끌어올렸다. LG는 다른 기업들이 한 라인에서 단일 제품을 생산하는 것과 달리 다양한 모델을 생산하는 ‘혼류’ 방식을 운용하고 있다. 냉장고 문을 부착하는 공정에서는 로봇팔이 20㎏에 달하는 문짝을 본체에 부착하는데, 라인 상단에 설치된 3D 카메라가 로봇팔의 눈 역할을 한다. 규격이 다른 다양한 모델의 본체가 라인에 도착하더라도 3D 카메라 촬영을 통해 로봇팔은 본체 결함 홈의 정확한 위치를 찾아 문을 부착할 수 있다. 이런 방식으로 1개의 라인에서 최대 58종의 모델을 13초당 1대씩 생산할 수 있다.
LG전자는 물류로봇과 전자팔 등을 도입해 전체 공정의 65%를 자동화했다. 이로써 현장 노동자들의 안전사고 위험도 크게 낮아졌다. 강명석 LG전자 키친어플라이언스생산선진화 태스크 리더는 “위험하고 까다로운 작업을 로봇이 맡고 작업자는 생산라인이나 로봇을 모니터링하고 관리하는 업무를 맡고 있다”며 “자동화의 목적은 무인화가 아니다. 창원 공장의 자동화는 결국 사람을 위한 자동화”라고 강조했다.
공장의 백미는 ‘디지털 트윈’ 기술로 완벽히 재현한 가상의 생산라인이었다. 디지털 트윈은 디지털 공간에 현실과 동일한 대상을 만들고 AI와 빅데이터 등을 활용해 다양한 상황을 분석·예측하는 기술이다. 대형 모니터를 통해 현재 가동 중인 생산라인과 부품 이동, 재고 현황, 설비 이상 유무, 제품 생산 실적 등을 한눈에 확인할 수 있다. LG전자는 30초마다 공장의 모든 데이터를 수집·분석해 10분 뒤 발생할 생산라인의 상황을 예측하는 시스템을 구축했다. 자재 소진을 예측하고 설비 이상 신호를 미리 포착해 대비하는 방식이다.
LG스마트파크는 제조 시설에 도입한 자동화·지능화·정보화를 바탕으로 지난 3월 세계경제포럼(WEF)이 ‘세계 제조업의 미래를 밝히는 공장’에 부여하는 ‘등대공장’에 선정됐다. 전 세계 103개 등대공장 가운데 한국 가전 기업은 LG전자가 유일하다. LG전자는 축구장 35개 규모에 달하는 스마트파크 1공장(대지 면적 25만 6000㎡)에 2025년까지 냉장고 생산라인 1개를 추가하고 오븐과 식기세척기 라인도 확대 구축한다. 스마트파크 2공장에서는 에어컨, 세탁기, 컴프레서, 모터 등을 생산하고 있다. LG전자 관계자는 “글로벌 생산거점에도 단계적으로 지능형 자율공장을 도입할 계획”이라고 말했다.
2022-10-11 17면
Copyright ⓒ 서울신문. All rights reserved. 무단 전재-재배포, AI 학습 및 활용 금지